Two Profiles IBR Roofing Panel Roll Forming Machine
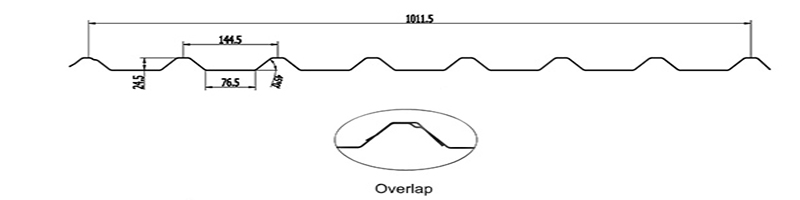
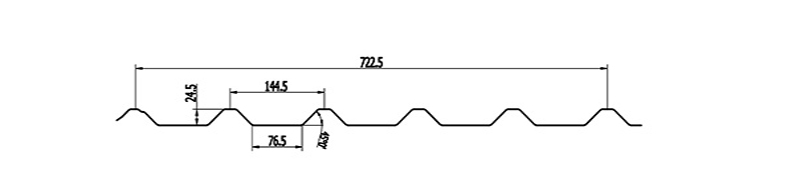
Work Follow
Decoiler→Manual Pre-Cutter→Guide Feeding →Roll Forming System→Hydraulic Post Cutter →Exit Rack
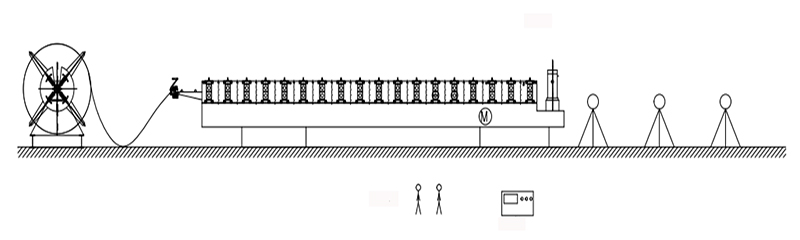
roofing panel roll forming machine
Machine Components
1) Manual Decoiler: one set
Un-powered, Manually control steel coil inner bore shrinkage and stop.Max Feeding width: 1250mm,coil ID range 508mm±30mm.
Capacity: Max. 5 Ton.
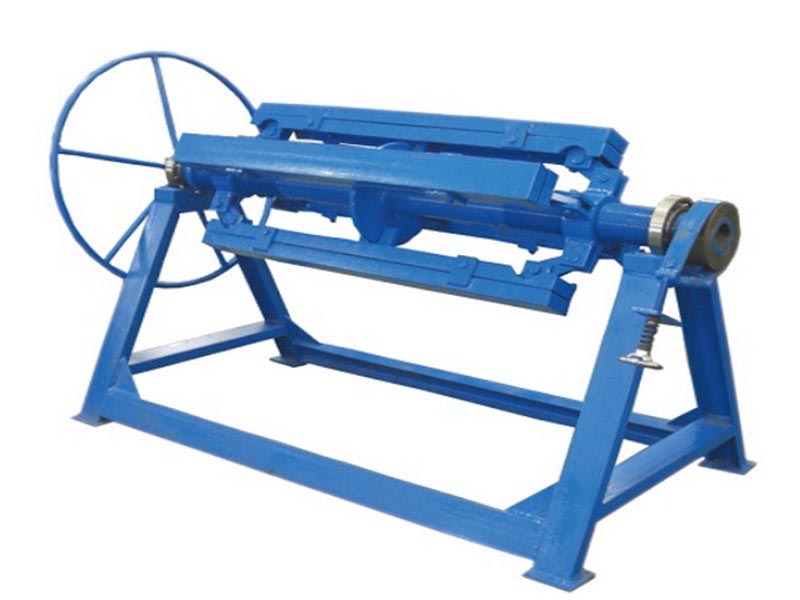
2) Manual Pre-Cutter
With manual pre-cutter for easy operation and save material:The pre-cutter is connected with PLC control system,PLC is calculating profile length within roll forming. Once
material is required to change,PLC is calculating the length for total quantity and remind operator production finishes and able to manual shearing material before roll forming so as to change material for new production.
It is the advanced function and good for production to save material, no waste.
roofing panel roll forming machine
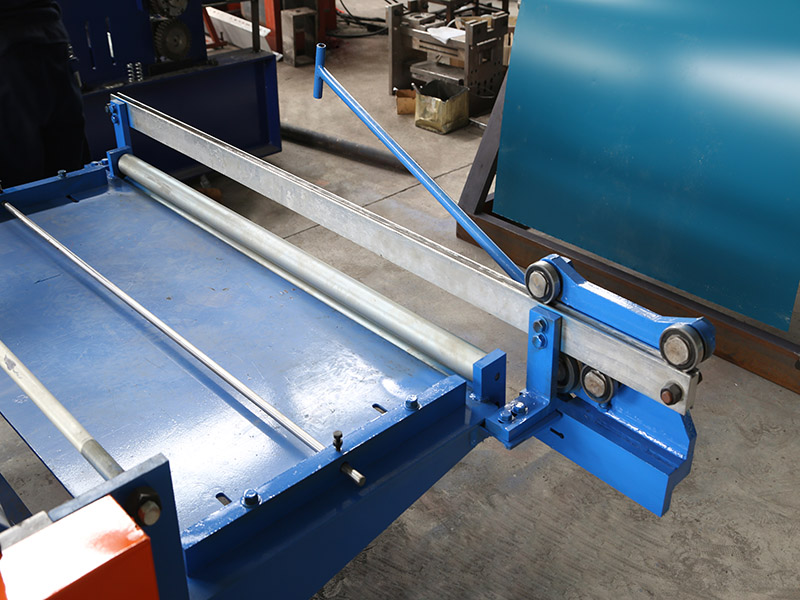
3) Main Machine
With feeding material guide, body frame made from H400 type steel by welding.
Side wall thickness: Q235 t18mm.
Rollers manufactured from 45# steel,CNC lathes,Heat Treatment,hard Chrome Coated,with thickness 0.04mm,surface with mirror treatment(for longer life and anti-rust).
Shafts Diameter=ф75/90mm,precision machined.
Main Motor=7.5KW,Frequency speed control.
Gear/Sprocket driving,about 18-step to form.
roofing panel roll forming machine

4) Post Hydraulic Cutting Device
Post to cut, stop to cutting,Two pieces type of cutting blade design, no blanking.
Hydraulic motor: 3KW.
Cutting tool material: Cr12MoV(= SKD11 with at least one million times of cutting life), Heat treatment to HRC58-62 degree.
The cutting power is provided by the main engine hydraulic station.
roofing panel roll forming machine
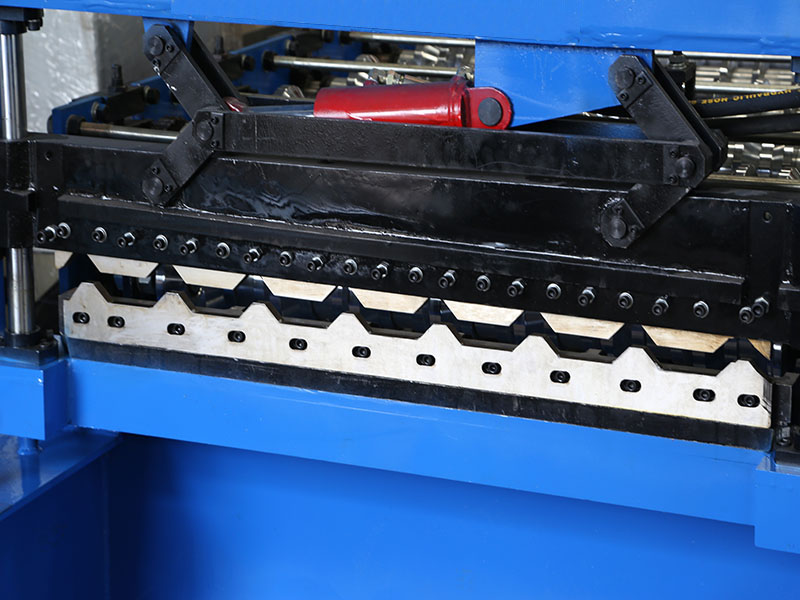
5) PLC Control System
Control The Quantity And Cutting Length Automatically.
Input The Production Data(Production Batch,pcs,Length,etc.)On The Touch Screen.
It Can Finish The Production Automatically.
Combined With: PLC, Inverter, Touch Screen, Encoder, etc.
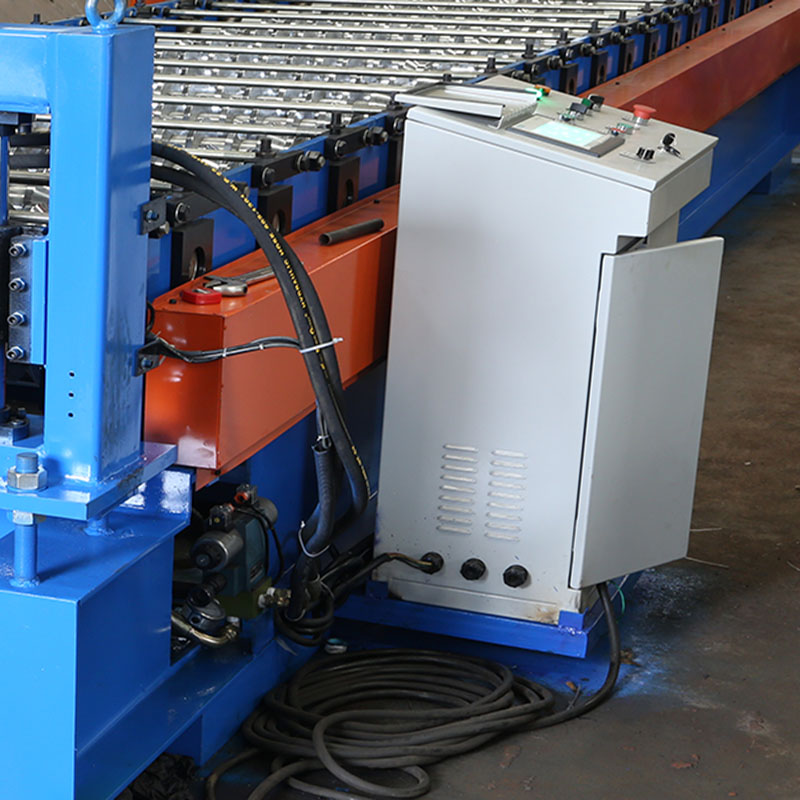